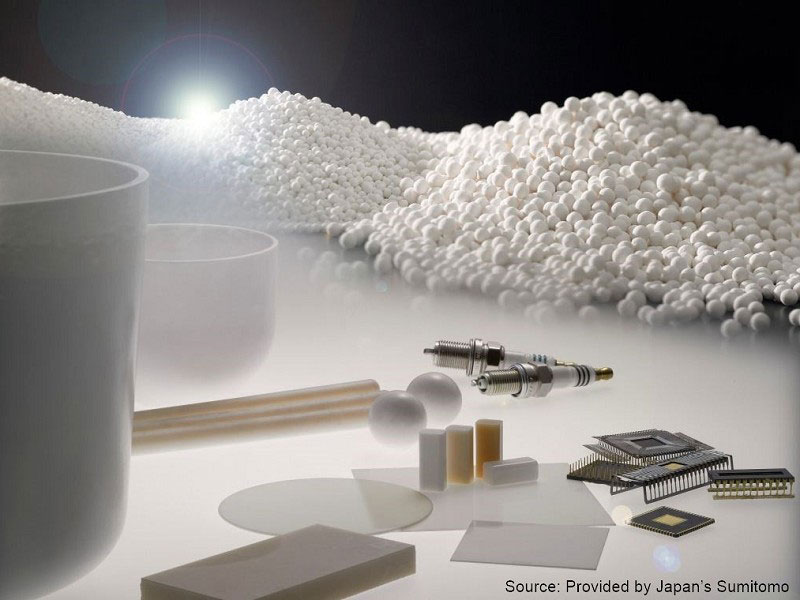
Zirconium Oxide Applied to Ceramic Product
Fine Ceramics, Advanced Ceramics, ZrO₂
At Touchdown, many medical and ceramic products have been manufactured using zirconium oxide due to its superior characteristics and advantages, especially when the zirconium oxide and metal are combined. Zirconium oxide's low thermal conductivity and high endurance characteristic can easily offset ceramic's easy to break disadvantage.
Zirconium oxide was found by Hussak in 1892. It exists in natural ore zircon sand or baddeleyite.
Pure zirconium oxide exists in the form of monoclinic crystal, cubic crystal and cubic lattice.
Zirconium oxide is characterized by high strength, high toughness, high hardness as well as excellent chemical corrosion and abrasive resistance.
The world's 80% zircon sand producing areas are concentrated in Australia, South Africa and the United States. The methods of refining zirconia from zircon sand include chlorination method and pyrolysis method. It can be used in fireproofing materials, dewaxing casting and high quality powders.
Major baddeleyite producing areas are concentrated in South Africa, Brazil and Soviet Union, and baddeleyite is mainly used in abrasive material and ceramic dye.
Zirconium oxide exists in monoclinic crystal at room temperature, and will be converted into square crystal phase as temperature rises to 1170°C and then converted into cubic crystal phase as temperature rises to 2,370°C, while cubic crystal phase will be dissolved into liquid phase at 2,680°C, the conversion from square crystal into monoclinic crystal is a martensitic transformation, and such phase conversion may produce 3 - 5% volume change, resulting micro cracks. Later, magnesium oxide, calcium oxide and other phase stabilizing agents are added to make sure that zirconium oxide can maintain the high-temperature stable phase, that is cubic crystal phase, which is called the stabilized zirconium oxide; if yttrium oxide phase stabilizer is added to keep partial square crystal phase, it can be called partially stabilized zirconium oxide.
Zirconium oxide thermal conductive ceramic ZrO₂ is pure white while yellow or gray containing impurities, and generally contains HfO₂, not easy to separate. The production of zirconia ceramics requires the preparation of narrow powder characterized by high purity, good dispersion performance, ultrafine particle and narrow particle size distribution. There are many methods to prepare superfine powder of zirconium oxide, and the purification methods of zirconium oxide mainly include chlorination and thermal decomposition method, alkali metal oxidation decomposition method, lime melting method, plasma arc method, precipitation method, colloid method, hydrolysis method and spray pyrolysis method.
Applications of Zirconium Oxide
Product Item | Required Characteristics | Used Material |
---|---|---|
Fresh cooking knife, textile machine tool, scissors, cutting tool | Toughness, strength and hardness | ZrO₂-Y₂O₃ |
Die, bearing, thread guide, grinding ball and other anti-abrasion parts | Toughness and hardness | ZrO₂-Y₂O₃ |
Sintering spacer and optical fiber connector | Thermal stability, insulation and toughness | ZrO₂-Y₂O₃ (TZP) ZrO₂-CaO ZrO₂-MgO |
Advantages of zirconia ceramics are as follows
1. It has high hardness, toughness and bending strength, and the density is between 5.95 - 6.05g/cm³. There are three kinds of ceramics produced by Touch-down, including aluminium oxide Al₂O₃, silicon carbide Sic and zirconium oxide ZrO₂, among which zirconium oxide has the highest toughness which is above 8MPa • m1/2.
2. It has high-wearing feature and low friction coefficient, whose abrasive resistance is 15 times of aluminum oxide ceramics while friction coefficient is only 1/2 of aluminum oxide ceramics. After abrasive machining, its surface smoothness becomes even higher and can reach above ▽ 9. It is in mirror shape and extremely smooth, and the friction coefficient is lower.
3. It has good insulation and strong corrosion resistance, is static-free, heat resisting and has excellent heat-shielding performance, whose coefficient of thermal expansion is close to steel.
4. It is self-lubricating and can solve the problem of pollution caused by lubricating medium and inconveniences added.
Processing form of Zirconia Ceramics:
1. Processing by Opening the Mould: Dry-type forming machine, CIM injection forming. CIP equalizing processing and plate cutting processing.
2. Shape Processing Product: Plane grinding shall be adopted according to customer interface requirements, as well as inner / outer diameter grinding, NC program processing and grinding and polishing.
Comparison of Main Performance Parameters of Zirconia Ceramics and Steel:
Material | Ceramic | Steel |
---|---|---|
Hardness (HV) | 1350 | 800 |
Thermal Expansion Coefficient (10-6/°C) | 9.5 | 11.5 ± 1 |
Sintering Temperature | 1550 - 2600 | 1200 - 1400 |
Temperature Resistance (°C) | 1800 | 1000 |
Specific Gravity (g/cm³) | 6.0 | 7.8 |
Flexural Strength (MPa) | 800 - 1000 | 2000 |
Young's Modulus (104Kgf/mm²) | 2.1 | 2.1 |
Poisson's Ratio | 0.3 | 0.3 |
Component Content (%) | ZrO₂ ≧ 94.5 | |
Color | Ivory, Black, Yellow | |
Puncture Voltage Strength (kv/mm) | 15 | |
Water Absorption (%) | < 0.01 | |
Compressive Resistance Mpa | 5000 | |
Hardness Hra | 88 | |
Volume Resistance (cm) | > 1012 | |
Roughness (µm) | ≦ 0.8 | |
Mirror Polish (Ra) | ≦ 0.05 | |
Thermal Conductivity (cal/cm.sec°C) | 0.007 | 0.13 |
Ceramics - Characteristic Comparison Table
Name / Characteristic | Aluminum Oxide (AL₂O) | Zirconium Oxide (ZrO₂) | Silicon Nitride (Si₃N₄) | Aluminium Nitride (AIN) | Silicon Carbide (SiC) | Boron Nitride (BN) |
---|---|---|---|---|---|---|
Appearance | Partial white or milk white or ivory | Ivory | Ash black | Brown | Black | White |
Dielectric Coefficient | > 1014 | > 1010 | > 1014 | > 1013 | > 106 | > 1014 |
Thermal Conductivity | 20 ~ 37 W/mk | 1.8 ~ 3 W/mk | 18 ~ 25 W/mk | 90 ~ 230 W/mk | 115 ~ 130 W/mk | 30 W/mk |
Coefficient of Thermal Expansion | 4.5 ~ 8 (10-6/k) | 8 ~ 11.5 (10-6/k) | 3.2 (10-6/k) | 4.5 (10-6/k) | 4.8 ~ 5.2 (10-6/k) | 1.5 (10-6/k) |
Young's Modulus | 380 (Gpa) | 210 (Gpa) | 300 ~ 320 (Gpa) | 320 (Gpa) | 400 ~ 420 (Gpa) | |
Poisson's Ratio | 0.27 | 0.3 | 0.26 | 0.25 | 0.19 | |
High Temperature Resistance | 1500° ~ 1700° | 550° / 1700° | 800° ~ 1300° | 1700° | 1700° | 2200° |
Resistance to Acid and Alkali | Strong | Strong | Strong | Strong | Strong | Common |
Magnetism | N/A | N/A | N/A | N/A | N/A | N/A |
Dimensional Stability | Slightly change with temperature | Slightly change with temperature | Slightly change with temperature | Slightly change with temperature | Slightly change with temperature | Slightly change with temperature |
Operating Centrifugal Force | Medium | Larger | Small |
HSY-3.0 Spec of Zirconium Oxide
Source: Provided by Japan's Sumitomo
- Related Products
Combination of High-Precision Ceramic and Metal
It is a compact, high-precision ceramic part manufacturer, who is specialized in the manufacture of fine ceramics / advanced ceramics / special ceramics...
Details